Additive manufacturing has become a keystone technology for high-precision manufacturing industries. It is also used to produce tooling, fixtures, and jigs to enhance traditional manufacturing processes by improving accuracy and efficiency. Additive manufacturing is ideally suited for producing precision-customized components for medical and dental prostheses and lightweight but robust aerospace components.
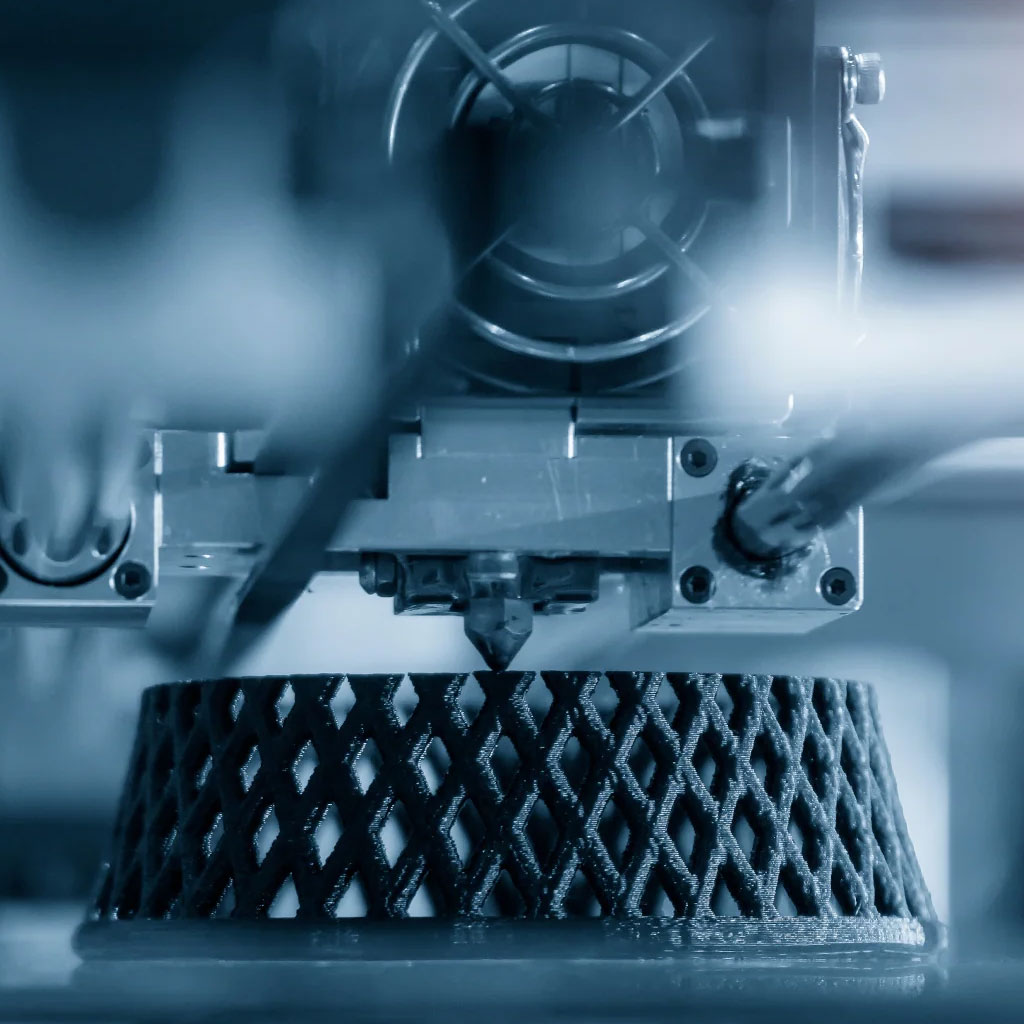
What is additive manufacturing?
3D Printing, or additive manufacturing, is swiftly becoming the benchmark process for precision-engineered aerospace components.
Much like domestic 3D printing devices, additive manufacturing works by layering materials to form three-dimensional objects. This differs from subtractive manufacturing, in which lasers or lathes are used to cut the desired shape from a solid piece of material.
Additive manufacturing can be used to manufacture intricate designs and accommodate diverse materials. With the addition of Direct Energy Deposition (DED) technology, these 3D printing techniques can be used to produce components with unmatched precision and complexity.
What is additive manufacturing?
3D Printing, or additive manufacturing, is swiftly becoming the benchmark process for precision-engineered aerospace components. Much like domestic 3D printing devices, additive manufacturing works by layering materials to form three-dimensional objects.
This differs from subtractive manufacturing, in which lasers or lathes are used to cut the desired shape from a solid piece of material.
Additive manufacturing can be used to manufacture intricate designs and accommodate diverse materials.
With the addition of Direct Energy Deposition (DED) technology, these 3D printing techniques can be used to produce components with unmatched precision and complexity.
What are the advantages of additive manufacturing for aerospace components?
How do we use additive manufacturing at SAB Aerospace?
Additive manufacturing frees us to work with a wide variety of metals, including stainless steel, titanium, aluminium, and nickel-based alloys, among others. Working flexibly with a variety of materials is essential in the aerospace components manufacturing sector because of the diverse and extreme atmospheric conditions in which they are used. It also allows us to fulfil custom orders for highly engineered precision products.
At SAB Aerospace, we use a Laserdyne 795XL metallic 3D printer with Direct Energy Deposition (DED) technology. The printer’s ample volume (1 cubic metre) means we can produce even large complex components to custom specifications with a speed, precision and efficiency that is impossible using other manufacturing techniques.
With its large volume and advanced DED technology, the Laserdyne 795XL elevates us to the forefront of advanced manufacturing. We are committed to pushing the limits of what can be accomplished with metallic 3D printing. We also hope to contribute significantly to innovation and progress beyond our industry.
What makes DED technology so suitable for aerospace components?
Additive manufacturing using DED technology offers several major advantages. This technology gives us a competitive advantage, not only over traditional manufacturing, but also over less advanced 3D printers. The Laserdyne 795XL allows us to produce intricate designs by depositing the chosen material layer by layer with a level of precision that is hard to match.
The ability to repair metal parts using DED technology additive manufacturing is another key advantage. Being able to repair or modify existing components ultimately extends the lifespan of components and reduces downtime.
DED technology is a highly cost-effectiveness and efficient way to manufacture aerospace components. Wasted materials are negligible as compared to subtractive manufacturing. This saves resources and protects the environment.