The structural stability of spacecraft depends on subsystems designed to endure stress, launch loads, freefall flight, and propulsion forces. Aerospace engineers grapple with the ongoing challenge of minimizing mass while preserving stability and enhancing strength.
SAB has also gained substantial experience in optical payload accommodation solutions. SAB Aerospace manages the entire process, from mechanical and sub-assembly design, manufacturing, and testing to the delivery of the final aerospace component ready for integration and launch.
Precision machining
SAB Aerospace has precision machining and chip removal capabilities. Once the engineering department has produced the designs, they are sent to the chip removal department, which uses CAM software to develop the process and simulate tooling and tool changes.
Finalised part designs are converted into machine language, and an aluminium block is precision machined. Simulated operations are replicated to remove material and produce a finished product according to the drawings.
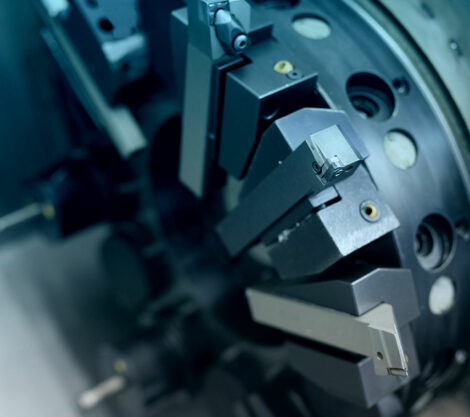
Between in-house equipment and equipment housed at partner test centres,
SAB Aerospace can perform:
- Mechanical testing
- Structural analysis
- Thermal analysis
- Space simulation tests
- Computational simulation
- Vibration and shock testing
- Thermal vacuum tests
- Static strength and stiffness tests
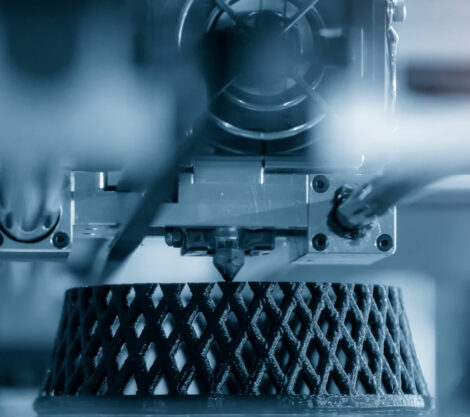
Additive manufacturing
Another key manufacturing technology SAB Aerospace uses is additive manufacturing a technology that has revolutionised high-precision manufacturing.
Integrating additive manufacturing into our design and production processes improves accuracy and efficiency.
Particularly well-suited for crafting customised, precision aerospace components, additive manufacturing makes it possible to engineer products that are lightweight and robust.
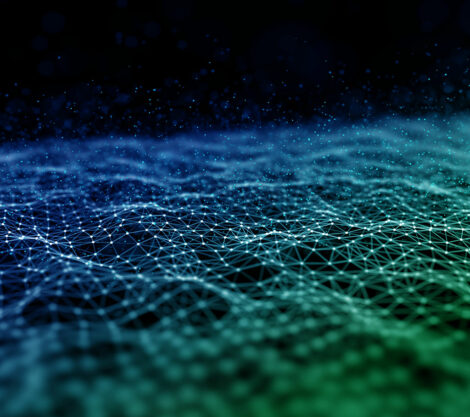
Innovative materials
Facing the uniquely complex engineering challenges presented by operating in space involves the inventive use of materials, strategic design, and advanced manufacturing techniques. SAB Aerospace engineers use lightweight materials and advanced structural design techniques to optimise the mass-to-strength ratio of its aerospace components.
SAB Aerospace engineers have gained in-depth experience in materials like aluminium and carbon-fibre-reinforced plastics. This experience has benefitted the optical payload programmes the company has been involved in, such as OPSIS (Optical System for Imagery and Surveillance), METIS (Solar Orbiter Instrument), and ESA’s EUCLID.
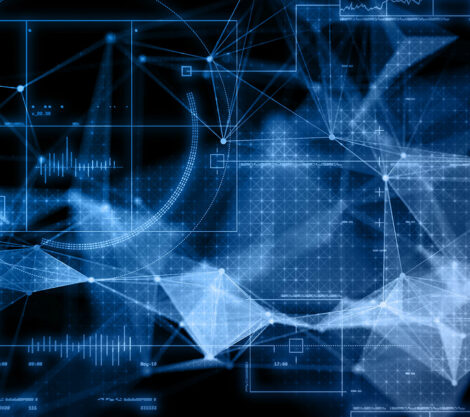
Design and modelling
Simulated models are used to analyse mechanical distortions resulting from shifts in temperature in orbit. The modelling process lets the company define limits and incorporate adequate tolerances into their designs. SAB Aerospace engineers use software programmes to check rigidity, strength, and stability requirements compliance.
The company uses MsC, NASTRAN (CAE tool/solver), HyperMesh (CAE/FEM pre- and post-processing), and Optistruct (structural optimisation and analysis). All the company’s design activities are based on 3D computer-aided design software, like Unigraphics NX.
The modelling process allows SAB Aerospace to fulfil the most challenging requirements of space programmes. Some of the company’s engineering achievements include participating in the mechanical design development of Galileo FOC, ExoMars 2015, and EDRS-C in partnership with OHB System AG.